Ce pas à pas présente un projet en cours de réalisation.
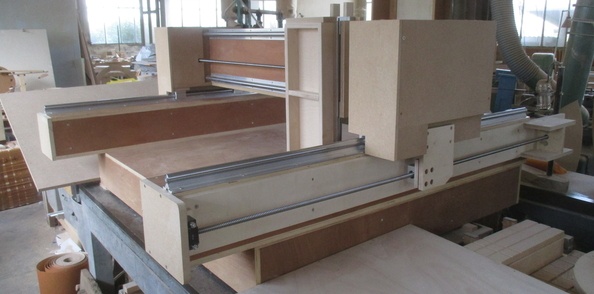
Cela fait pas mal de temps que je réfléchis à construire une CNC, destinée à la découpe de panneaux de contreplaqué et un peu d'aluminium. La surface de découpe devrait être de 1mx1m. La structure sera réalisée en bois.
Si je sais à peu près travailler le bois et ai quelques notions de mécanique, je n'ai aucune expérience en matière d'électronique et de motorisation.
Ce projet est un travail d'équipe interdisciplinaire, réalisé en étroite collaboration avec le FABLAB du Creusot UTOPI, qui a bien voulu me suivre dans l'aventure et le Crealab de Montceau les mines, l'ALTERNATIVE, qui a beaucoup travaillé sur la partie électronique et le pilotage.
Liste des articles
- Pourquoi en bois ?
- Principes généraux
- Construction du bâti:
- Guidage: les rails supportés SBR
- La boite pour l'axe Z
- Réception des rails supportés
- Installation des rails sur le portique
- Installation des rails sur les longerons et du portique:
- Installation du portique
- Consolidation du portique:
- Un peu d'histoire
- Habillage
- Installation des vis d'entrainement
- Voila, ça marche!
- Terminée!
- En production
- La liste des courses à faire...
- Inauguration
Pourquoi en bois ?
Cette machine sera réalisée en bois. Je vois déjà les sourcils qui se haussent. Pourquoi donc ? eh bien, tout simplement car le bois est un matériaux qui absorbe bien les vibrations, en tout cas, mieux que le métal.
Ce ne sera bien sur pas du vrai bois d'arbre, mais un contreplaqué de qualité, de hêtre ou de bouleau, beaucoup moins sensible à l'hygrométrie.
J'ai eu dans le passé un peu de mal à convaincre certains, tenants du tout métal. Je viens enfin de trouver la démonstration physique.
Il se trouve que la capacité d'un matériaux à transmettre les vibrations est mesurée par un coefficient, le Loss Coefficient (je n'ai pas le terme en français). Et comme on le voit sur ce graphique, le "loss coefficient" du bois est de l'ordre de 10-2, alors que pour les métaux , c'est de l'ordre de 10-3 à 10-5 (plus le coeff est petit, plus cela transmet).
Donc, les métaux serait 10 à 1000 fois plus "vibrants" que le bois, toutes choses égales par ailleurs. Exception faite de la fonte (équivalente au bois), mais je n'ai pas la capacité à fondre de la fonte...
Certes, le bois est bien moins rigide que l'acier ou même l'alu, mais dans ce cas, il suffit de déterminer des section plus grandes, de manière à compenser. Cela se calcule. C'est une simple question de moment d'inertie.
Principes généraux
La forme générale est la plus ramassée possible, de manière à minimiser les flexions résiduelles.
La base cloisonnée fera 1,4 x 1,4 m et 20 cm d'épaisseur.
Les longerons en x auront une section de 17x14 cm, la traverse en Y (le portique), fera 28 x 25 cm
Comme la machine sera destinée à découper du cp, on n'a pas besoin de beaucoup de hauteur en Z.
Le budget pour ce projet étant très limité, nous étions partis à l'origine sur un système de guidage avec des roues en V et des cornières alu.
Mais il se trouve que j'ai trouvé un fournisseur de rails supportés (rails SBR) pas trop cher, en tout cas, bien moins cher qu'auparavant. Ce système est bien plus rigide, robuste et éprouvé.
La motorisation devrait se faire avec des courroies crantées, prises entre 3 poulies crantées.
Afin de bien protéger les courroies et les rails SBR des poussières, un cache en demi tunnel amovible relevable sera fixé au dessus.
La partie gris clair, au milieu, sera amovible, de manière à pouvoir éventuellement y placer des pièces plus épaisses que du cp.
De même à l'avant, la broche pourra s'avancer au delà du plateau, de manière à pouvoir usiner des pièces sur chant ou placées verticalement (par exemple, une mortaise ou des queues d'aronde ou des tenons). Un étau moxon pourra y être adapté.
Détail du mécanisme de guidage:
On voit à gauche le rail supporté SBR bleu foncé, et l'un des blocs coulissant sur billes, encastré dans la structure en bois pour éviter les flexions.
La tête de fraisage:
Elle coulissera également sur des rails supportés SBR, et une vis sans fin actionnée par le moteur en haut permettra d'actionner la montée/descente.
Il faut faire en sorte d'avoir un ensemble le plus compact possible, de manière à limiter le porte à faux et les flexions au niveau de la tête de fraisage.
Construction du bâti:
Voici la réalisation du bâti. En contreplaqué de 15 mm. Tous les caissons sont réalisés comme des boites de torsion, avec cloisonnement à l'intérieur, collé/vissé.
L'ensemble fait 160 cm de large, 140 en profondeur.
Coût du bâti bois: 140 €
Guidage: les rails supportés SBR
Voici les rails SBR trouvés en Allemagne pour un coût très raisonnable: 237 € fdp compris, pour les 2 rails de 140 mm et 2 rails de 120 mm en 20 mm de diamètre et les blocs de coulisse pour les axes X et Y
Cela revient en fait pas beaucoup plus cher que la solution profilés à rainures / petites roues, et c'est bien plus rigide et éprouvé:
Réception des rails supportés
Je viens de recevoir les rails. Je ne résiste pas à mettre des photos. Ils sont superbes, cela respire la belle mécanique. Tout est bien lisse, bien droit, et cela coulisse parfaitement sans jeu. A voir au montage...
Installation des rails sur le portique
Je vérifie que la surface du portique où seront fixés les rails est bien plane, et non voilée/tordue. Pour cela, je la pose sur mon grand marbre. Parfait, c'est bon, le portique n'est pas tordu.
Je fixe un rail avec des vis aux extrémités. Pour le second, afin d'être certain du parallélisme, j'utilise bêtement un gabarit, un morceau de cp de longueur correspondant à l'écartement des rails. Je visse le rail d'un coté, puis l'autre extrémité, en plaquant le rails contre le gabarit. Normalement, cela devrait être parallèle.
La fixation du chariot supportant l'axe Z sur ces rails n'est pas si évidente. On fixe les blocs coulissant avec des vis, mais il faut être certain du bon positionnement des trous, des entraxes, etc. Comme je n'ai pas encore de cnc, difficile à la main de faire quelque chose de très précis. Or, cela doit être extrêmement précis! il ne faut pas que les blocs coulissants soient de travers...
Je procède donc en plusieurs étapes:
- Je visse sur chaque bloc une plaquette en cp, chaque bloc restant indépendant.
C'est ensuite sur ces plaquettes "en situation" sur les rails, que je colle la grande plaque, en la positionnant de manière à ce que le bord soit bien perpendiculaire aux rails. Je m'aide pour cela d'une équerre sur 2 axes.
Je fixe l'ensemble avec des serre-joints et je teste le déplacement. Cela coulisse bien sur toute la longueur!
Je peux donc coller définitivement la plaque sur les plaquettes, le tout positionné avec des serre-joints. Je vérifie que cela coulisse toujours aussi bien. C'est parfait, pas de point dur, pas d'endroit où cela force.
J'avoue que je suis bien content...
Et voila le portique et son chariot:
Installation des rails sur les longerons et du portique:
L'installation des rails sur les longerons est un peu plus compliquée, car c'est plus grand... La moindre erreur sera amplifiée...
Je vais suivre la même méthode que pour le portique:
Vérification de la planéité des longerons: Je les place sur le marbre, face recevant les longerons contre la surface du plateau. C'est bon, ils ne sont pas voilés.
Vérification de la planéité de l'ensemble base + longerons. Je place la base sur le marbre sur 4 cales aux 4 coins, les longerons dessus, puis les rails.
Avec une règle, je vérifie que la hauteur aux 4 coins est la même par rapport à la surface du marbre. C'est bon.
- Collage des longerons sur la base:
- Fixation des rails:
Je fixe aux deux extrémités un des rails:
Avec un simple liteau coupé à la bonne longueur, je fixe une extrémité de l'autre rail. Puis, avec la latte comme butée, je positionne l'autre extrémité du rail, et je visse dans le longeron. Les 2 rails sont théoriquement parallèles.
Pour installer le portique sur les rails, je procède en plusieurs étapes.
- Comme pour le chariot du portique, je visse des plaquettes de cp sur chacun des blocs coulissants sur les rails des longerons:
Je fixe ensuite sur ces 4 plaquette, un grand plateau ayant la forme du portique et des ses contreventements.
Ce plateau doit être bien perpendiculaire aux axes des rails des longerons. Pour cela, j'utilise une grande équerre fabriquée spéciale, qui s'adosse à l'un des rails et sur laquelle va buter le plateau.
Je fixe le plateau sur les plaquettes et je vérifie que cela coulisse bien. Miracle! Banco! Cela glisse sans accroc!
Je peux donc définitivement coller le plateau sur les plaquettes et donc, sur les guides coulissants. Je vérifie à nouveau que tout glisse bien. C'est parfait, l'ensemble se déplace avec un doigt, pas de frottement, pas d'effort! Je suis content content!!
Je pourrai demain placer le portique sur le plateau.
Installation du portique
Et voici le portique installé. Tout coulisse bien, j'ai passé la matinée à m'amuser à faire bouger la machine dans tous les sens...
Consolidation du portique:
La poutre transversale a été collée/ vissée sur la plaque de mdf qui reliait les 4 patins coulissants. De même pour les deux "boites" latérales.
Il restait à consolider tout cela par des contreventements ad hoc:
Une plaque double de mdf verticale prolonge la boite sur le coté et fait office d'équerre de maintien:
IL faut également consolider autour des patins coulissants, de manière à ce qu'ils n'oscillent pas latéralement:
Deux épaisseurs de contreplaqué sur la longueur, et deux blocs accoudés contre les blocs font en sorte que les patins sont à moitié encastrés.
Et voila l'ensemble. Le tout est extrêmement rigide dans tous les sens, et cela coulisse toujours aussi bien!
Un peu d'histoire
Il est à noter que ce projet de CNC a une histoire familiale.
Mon père était modeleur. Il réalisait des modèles pour les fonderies, sur de vieilles machines qui n'avaient bien sûr aucune électronique.
Dans les années 70/ 80, il a commencé à parler de certains de ses collègues qui investissaient des fortunes dans les premières machines numériques, pilotées pas un ordinateur. Mon père n'en voyait pas l'intérêt, et il a continué de travailler à l'ancienne. Il a sans doute eu raison, car les collègues indépendants qui avaient investi dans ce genre de machine, ont disparu, seuls quelques uns ont survécu, la plupart balayés par la concurrence des pays de l'est dans les années 80, puis par la Chine et l"évolution rapide des technologies. Mon père a continué tant bien que mal jusqu'en 2001, à 70 ans.
Cette CNC de bricoleur, réalisée avec du simple contreplaqué, pour quelques centaines d'euros, est donc comme une revanche ou un pied sde nez à l'histoire. Mon père, qui a 88 ans, pourrait faire des modèles avec cette machine "pilotée par un ordinateur"...
Habillage
Avec tous ces rajouts et conteforts, cela faisait un peu bricolé.. J'ai donc tout habillé pour faire plus net.
.....
Installation des vis d'entrainement
Après une longue pause, je reprends la construction de la cnc bois.
Je pensais à l'origine réaliser un entrainement par courroies. Mais la difficulté de trouver la "bonne" courroie, et le fait que ce n'est peut-être pas le système optimal (la courroie peut se détendre, il faut les changer de temps en temps), m'ont fait me tourner vers un entrainement par vis à billes, d'autant plus que l'on trouve maintenant des vis par trop cher.
Coût total: 200 € pour 3 jeux de vis 1500 mm et une de 350 mm (axe Z)
fr.aliexpress.....27426c37MUUQXR
Voici donc l'installation. C'est sur cet entrainement que repose une bonne partie de la précision finale. Il ne faut pas, en effet, qu'il y ait le moindre jeux ou des flexions dans le système, car cela a un impact direct sur les déplacements, donc, sur la précision.
Il faut également que les vis soient bien parallèles aux rails, et que les "noix" d'entrainement se soient pas de travers, sinon, cela coince...
Pour l'instant, l'estimation des coûts est la suivante:
- Bois: 140 €
- rails SBR: 237 €
- vis à billes: 200 €
Total: 577 €
Il restera:
- 4 Moteurs pas à pas: 100 à 200 € (en fonction de la puissance)
- Electronique: 300 €
Le total devrait donc être autour de 1000 € pour une machine de 1mx1m de surface de travail (hors broche, pour laquelle il y a tous les prix, à partir de 200 €...)
.......
Voila, ça marche!
Après de nombreuses années d'efforts, de doutes et d'enthousiasmes, le -Comité-Spécial-Intercompétences-pour la Construction-d'une-CNC-en-Bois a l'immense honneur et la joie de pouvoir annoncer que la Machine CNC en bois fonctionne et qu'elle a réalisé ses premiers copeaux!
La machine n'explose pas en plein travail, ne perd pas de pièces, ne se tord pas sur elle-même. Elle vibre très peu, les mouvements sont fluides et doux.
Le premier essais, un grand triangle gravé, montre que l'équerrage et le calibrage des déplacements sont bons.
Il restera bien sur à peaufiner tout cela, mais une grande étape a été franchie!
C'est un petit pas pour une CNC, mais un grand pas pour nous tous!
Voici donc une grande CNC, de 1m x 1 m, qui a coûté moins de 1000 €!
Merci aux Grands Bidouilleurs du Fablab L'Alternative, à Montceau les mines, pour leur grande et sympathique implication dans ce projet!
.....
Terminée!
Voici la machine dans son état "terminé" (en attendant les futures modifications...).
Avec les boutons d'arrêt d'urgence, l'aspiration, etc...
En production
J'avais toujours dit que cette machine ne servirait pas à la réalisation de pièces pour mes télescopes, et puis, exceptionnellement, parce que j'avais une commande très urgente, on a fait quand même l'essai avec.
Les test est concluant: 15 h d'usinages, 127 pièces de toutes tailles, bien compliquées, et elle a bien résisté. Tout est d'équerre, les pièces s'emboitent bien les unes dans les autres. Après ébavurage, tout est propre et net.
Tout ça, avec une affleureuse sur 3 bouts de bois! Et le tout pour moins de 1000 €. Qui dit mieux ?
(Au fait, j'ai envie de l'appeler Pollux, devinez pourquoi...)
La liste des courses à faire...
Je me suis amusé à faire la liste non exhaustive des choses que je ferai un jour avec la Machine...:
Sphère / dome geodésique
Plan 3D de notre région,
Haut parleur back horn
Base pour platine disque Lenco (remplissage pour éliminer les vibrations)
Iris en bois
Spirographe
Kimiko (panneaux découpés, motifs japonais) /moucharabieh,
Maquette dirigeable / avions
Machine cinétique, horloge,
Ampli passif
Manches couteaux
Moteur à piston en bois
Fontaine / Horloge à billes
Tongue drum
La machine à musique de Wintergaten...
Vélo en bois
Guitare électrique
Jeu d'échec avec plateau 3D
Theo Jansen sculptures mouvantes
Calendrier cryptic
Caravane tear drop
Chaise pliante (encastrée), meubles flat pack
Etabli en kit
Etau en kit
Astrolabe
Sphère armillaire
Harpe celtique
etc, etc, etc...
Inauguration
Et voici la video de l'Inauguration Officielle, avec les membres des Fab Lab Utopi et l'Alternative:
Ce pas à pas présente un projet en cours de réalisation.
Discussions
wahou projet ambitieux a suivre !
Un simple avis les gars, la vibration maitrisée c'est une chose, la déformation incontrôlée c'en est une autre,, le bois c'est le bois, tu peux faire ce que tu veux ça finira par bouger dans tous les cas, maintenant si tu n'a pas besoin de travailler au micron, ça va. Les machines CNC au top à 2 boules d'euros, et voir plus évidement, ne sont pas en bois, je pense pas que se soit pour le côté philanthropique de la foret. Au final, du coup , ça dépend de ce que tu veux produire, et avec quelle précision.
+1
Mais bien sur, bien sur... :)
On se croirait sur Usinages.com et les copains métalleux...Je connais, j'ai donné.
Il se trouve que je travaille un peu beaucoup le cp pour des choses qui sont censées ne pas trop "bouger" (va voir mon profil). Je sais un petit peu comment ça marche. Toute la structure sera sous forme de boites de torsion, avec parois internes. Cela ne devrait pas trop se déformer. D'autre part, un cp de qualité bougera peu.
Bien évidemment, la précision attendue n'est pas le micron...
Enfin, si cela bouge (hygrométrie), sur du cp, cela bougera de manière homothétique.
Enfin de enfin, ce n'est pas la première cnc qui sera réalisée en bois... Y en a plein, suffit de googler... Holzfraese, Builtyourcnc, etc... Z'ont pas l'air d'être si cons que ça, c'est gars là...
EN tout cas, merci d'être passé.
Ce n'est pas une critique, juste un avis, comme indiqué, mais je reste persuadé que personne ne puisse contrôler les forces de la nature, induites celle des réactions bois, y compris sur 3, 4, 5 ans en tenant compte d'une condition Température, Hygrométrie constante et controlée. Pour ce qui des utilisateurs de "Méga-CNC" en bois, t'imagine bien , normal, qu'il ne vont pas publier le fait qu'il se soient lamentablement planté sur leur choix de structures CNC, vu qu'ils sont largement "nourrit" par certaines marques de CNC...Aprés...
Entre du cp de qualité et un MDF, ou MDF amélioré, qu'est ce qui est le moins sensible aux variations d'hygrométrie ?
Et même si ça bouge, est-ce bien grave ?
Ce qui compte, c'est que la structure ne se déforme pas comme une patate avec les changements de conditions météo et qu'en gros on garde les parralélismes et perpendicularités importantes.
Après, que des longueurs varient, ça arrive surement sur tout un tas de machines avec la dilatation thermique. Ce qui compte ici, c'est que quand on demande un déplacement de 10mm, on obtienne un déplacement de 10mm, et ce quel que soit le jour de l'année (et l'hygrométrie puisqu'on en parle). Je pense qu'on peut concevoir de tels mécanismes: si dans le cas présent la courroie ne change jamais de longueur, alors c'est bon.
Et puis si les dimensions de la machines varient pendant l'usinage (au cas où on usine pendant 3 semaines avec gros changements météo), ben c'est sûr on peut rien y faire !
Kentaro: D'après les charpentiers de marine avec qui j'ai eu des contacts, il suffirait de noyer le CTP dans une résine époxy (ahah comme sur mon boat) pour stabiliser le bois (plus de variation d'hygrométrie et rigidification de l'ensemble)
Est-ce une piste ?
Normalement, un cp de qualité peut varier de 1mm sur une largeur de 120 cm. On est donc sur une variation de 1/1000... Cela devrait aller.
Joli projet en vue !
Je pense que cela est tout à fait réalisable en panneaux bois.
L’acier aussi se dilate il me semble, de l’ordre de 0,012mm / mètre / °C (soit 0.25mm sur 1 mètre pour 20°C d'écart)!
Quelques points si tu me permets :
→Ne faut-il pas que tu allonge ta table (ou du moins tes supports + rails) sur l’axe X vers l’arrière. De manière à ce que tu aies bien une surface d’usinage de 1000x1000mm. La broche étant déportée au devant du portique.
→Pour le réglage des roues en V, oui généralement on excentre légèrement le perçage de fixation de l’axe support. J’ai bien compris que tu souhaitais faire autrement. Autre solution, que ce soit le rail du haut sur ton portique qui soit réglable (perçages de fixation oblong) mais faut être précis pour la fixation des roues en V sur le chariot broche.
→Avec ce genre de conception (broche en applique sur poutre portique) et ce système de guidage (roues en V sur cornières V) il faut faire attention à ce que le portique ne bascule pas. Et donc bien équilibrer et peut-être élargir les supports du portiques (et allonger donc encore un peu l’axe X).
Aurelien - Mobbler +1 pour l'équilibrage dynamique du portique afin de minimiser le couple de basculement lors des mouvements du portique
Merci Aurelien pour tes commentaires.
Je suis preneur de toutes les idées et commentaires, notamment en matière d'ergonomie, de la part d'utilisateurs.
Ah, ok pour le dernier point. Je n'avais pas compris que tu avais prévu 4 roues de chaque coté du support. Je croyais que le rail bleu du bas (le long des X) était la transmission.
D'ailleurs as-tu déjà définis la transmission: crémaillère ou vis à bille?
Je pensais utiliser des courroies crantées pour la transmission. Peut-être un système a double courroie (qui s'imbrique l'un dans l'autre, sauf au niveau de la poulie moteur, de manière à réduire les tensions sur la courroie).
loss coefficient = (littéralement) coefficient de perte
Pour un matériaux, je dirais plutôt coefficient d'amortissement : plus l'amortissement est important, moins les vibrations se propagent loin/moins les vibrations durent longtemps dans le matériau.
Ah ben voila un projet que je vais suivre avec attention ! Merci pour le partage...
JE vais régulièrement en Saone et Loire chez mes beaux parents et cherche toujours un prétexte pour m'échapper... si tu veux bien, je m'inviterais volontiers pour un café !
Ah si tu passes par chez moi, ce serait un très grand plaisir de te rencontrer!
J'espère que tes beaux parents ne liront pas ton poste lol... Mais saches que je te comprend. Lol
Olivier, suis aussi en Saone-loire, avec plaisir pour le café à la maison !
HOUA!! ça c'est un projet de dingue que je vais suivre avec attention. Car des projets complexe comme ça j'adore. bon courage pour réaliser ton projet.
Ça c'est un chouette défi. Et puis je suis d'accord,le bois peut absorber les vibrations mieux que le métal. Y a qu'à voir quand on tape sur un établi en métal ou en bois, le résultat n'est pas le même. Le bois absorbe.
Puis le métal ça ne se travaille pas de la même façon que le bois
C'est certainement une bonne idée qui personnellement m'intéresse en tant que débutant.Je vais suivre le projet.
Bonjour’ peut être que ce lien peut donner des idées, à voir!
youtube.com/pl...9TgjUzQRI4Z3gHQ
paoson.com/en/...g/3d-router-n17
Oui, en effet, ce n'est pas une cnc, mais il y a plein d'idées!
Mise a jour: réalisation du bâti
Super projet, je crois que la conception de votre CNC est suffisante pour l'utilisation que vous en ferez. usiner du bois ou du cp avec une fraise hélicoïdale ne feront pas supporter de contraintes importantes au bâti.j'ai utilisé ce type de fraise sur,une défonceuse, et j'ai été agréablement surpris par le peu de résistance par rapport à l'utilisation d'une fraise droite.
là y a déjà du taf !!!
La, c'est le plus simple, même si on voit tout de suite à quoi cela va ressembler... Maintenant, il va falloir faire les alignements des rails, pour que tout soit bien parallèle et orthogonal. Cela ne va pas être si facile...
L'électronique est en cours, réalisée par le Fablab du Creusot, à base d'arduino, et piloté par GRBL.
je suis vraiment curieux de voir ce que vont donner ces rails...
Ils ont l'air costaud...
Auriez-vous les spécificités des rails? Je ne maîtrise pas du tout l'allemand..
La page traduite: kampundkoetter...earfuhrung.html
Vu de loin, cela ressemble à un rail SBR supporté habituel souvent utilisé pour la réalisation de grandes CNC. Reste à voir comment il a été usiné, et la précision de la douille...
En fait, si on achète directement en Chine, ces rails ne sont pas très chers, mais c'est le coût du transport qui double le prix. Je suppose qu'un importateur en Allemagne en a fait venir quelques containers, et cela réduit pas mal le coût.
Merci pour le lien.
Je suis curieux d'avoir le retour une fois les rails livré...
à suivre...
vivement qu'on la voit en action. Super projet ! je suis ton pas à pas avec intérêt. Merci pour toutes ces informations.
Génial, ça avance bien..
Ça avance bien par ici
L'Atelier Vosgien Oui, mais bon, cela va être un tank... Si j'en fait une autre, elle sera peut-être plus comme la tienne! :)
bonsoir vous avez fini votre cnc ?
non, c'est un reportage en direct des studios, du "live", plein de bruit et de fureur, plein de sang et de larmes.. :) .
Tout le suspense, c'est quand on va mettre un bout de bois sous la fraise, et ce que cela va donner... ;)
Ça avance bien , ton électronique est prête ?
Oui, pour l'électronique, c'est le fablab du Creusot, Utopi, qui travaille dessus. Ils viennent de remettre en route une ancienne Charlyrobot dont la carte avait grillé. Le contrôleur est réalisé à partir d'Arduino.
C'est surtout pour le fun, car un contrôleur ne coûte pas grand chose...
On devrait donc terminer la partie mécanique et la partie électronique en même temps.
Kentaro Moi la partie electro est terminé , il me manque juste des profilés qui viennent de chine est qui traînent en route :( facebook.com/L...29670837221086/
Ça v en faire du poids pour chaque moteur! Mais ça fait plus fini
Cela ne rajoute relativement pas grand chose, et cela coulisse toujours aussi facilement.
Belle réalisation !tu vas avoir une belle machine ! qu'a tu prévu comme moteurs et interface ?
Pour les moteurs, j'ai découvert qu'il ne fallait pas simplement regarder le nom, nema 17, 23, 34, mais le couple.... et pour le même nema 23, on a des couples qui vont de 100 à 400 n.cm... j'ai trouvé celui, qui me semble bien puissant:
fr.aliexpress....#3468#15608#187
Pour l'électronique, c'est en cours de développement par le Fablab voisin du Creusot, avec un arduino.
Kentaro Pour l'elec, si tu as besoin, n'hésite pas, j'ai déjà beaucoup testé également, et j'ai une solution qui fonctionne comme un charme depuis 5 ans... un arduino nano qui gère mes 4 nemas (la cnc que j'ai construite est une 4 axes, alu par contre) + 4 pilotes dont je ne me souviens plus la reference, mais c'est facile à retrouver, et un raspbery qui permet de passer toutes les infos et de pouvoir la piloter en wifi directement de mon bureau, avec une camera de surveillance.
quelle lumière, superbe atelier, fais tourner la cnc!
C'est propre l'ajout des vis d'entraînement. C'est fou ce que tu arrives à faire avec du contreplaqué. J'attends la suite avec impatience.
Magnifique projet, dont je vais m'inspirer ! Où en es tu de la partie électronique ?
toitetmoi Très bonne question... Cela a pris du temps, avec les restrictions covidiennes, etc... La partie électronique et les moteurs ont été montés et fonctionnent à blanc, et le tout va être installé prochainement sur la machine. Je croise les doigts!
Quand tu en auras le temps, si tu arrives à documenter la partie électronique et moteurs, ça m'intéresse beaucoup. Ton concept de structure en contreplaqué me semble très intéressant, je vais te copier je pense
En tout cas, merci beaucoup pour tout ce que tu partages, me fichier de calcul des diedres est très bien pensé. Je savais résoudre le problème par le trait, et par la trigonométrie,mais je n'avais jamais songé par les maths et le produit scalaire
toitetmoi Merci! Oui, le truc du produit scalaire, c'est assez puissant comme outil...
Pour avoir déjà suivi le même process (en ayant commencé beaucoup plus petit), je peux t'aider si tu veux/en à besoin sur la partie arduino/GRBL, et même un peu plus loin puisque j'avais mis un RASPI avec écran tactile qui envoyait à l'arduino et qui etait relié à mon réseau pour pouvoir envoyer directement depuis mon PC de travail. ma première était en 30x20, ma seconde en alu 60x40 et j'ai maintenant une 120x60... Conseil rapide, prend tout de suite une bonne broche (genre 2kw) avec les plus petites, tu bloques assez vite si tu veux faire du travail serieux. (d'ailleurs si certains sont intéressés, ma 60x40 est à vendre).
L'atelier de Fred Merci pour ta proposition. J'aurai peut-être besoin de tes conseils! De plus, Roanne, ce n'est pas très loin de Montceau les mines! Il faudra que je vienne te voir (ou inversement).
" Et pourtant elle marche" bravo de nous avoir montré que la ténacité paie
wil68 Merci! En fait, ce n'est pas de la ténacité... C'est moi qui ai été très long pour construire le bâti, et puis ensuite, il a fallu trouver les bonnes personnes pour l'électronique.
Très belle réalisation qui t'a demandé pas trop d’investissement en espèce mais beaucoup en temps je suppose. Est ce que peut peut y mettre un graveur laser ?
Bon courage pour la suite.
YvesR Cela a pris beaucoup de temps pour réaliser le bâti, car j'ai été très occupé par ailleurs. En fait, si on additionne le temps réel, ce n'est pas grand chose, quelques semaines seulement (ce sont des caissons, et ensuite, il faut fixer les rails et les vis d'entrainement). Pour la deuxième cnc (cnc2) en cours, j'ai mis 3 jours pour faire le bâti...
On peut y mettre un graveur laser, en effet.
merci pour ta réponse
En dépit des grincheux, tu l'as fait! Un grand bravo. C'est un sacré challenge et je t'envie de l'avoir réussi avec sans doute aussi l'aide de ton fab-lab.
TyCoat Merci! Mais en effet, sans le fablab, elle n'aurait jamais fonctionné... Ce fut vraiment un travail d'équipe.
C'est une grosse erreur ! Le bois ça va travailler et se tordre !
!
Naaannnnn.j'te taquine
Chouette et très content pour toi.
Tu vas découper tes pièces de télescopes avec ?
Ben moi, je dis que le bois, c'est le meilleur truc du monde! Y a pas mieux pour faire une cnc!
Je vais continuer de faire découper les pièces des télescopes par un sous-traitant, qui fait cela très bien. Cette machine n'est pas destinée à un usage professionnel et intensif. Eventuellement pour faire des prototypes, et plein de petites choses par ailleurs.
Le plus compliqué, quand on a une cnc, c'est de trouver les idées pour l'utiliser à bon escient...
héhé la première cnc sur batterie, meuh non
ca le fait, classe portique, envie de suivre la suite
mofran On changera la fraiseuse un peu plus tard. On verra.
Kentaro ben oui , c'est un clin d'oeil. ca serait dommage d'être limité par la puissance de la broche , ca fausserait les tests
pour info j'ai vu que un modèle + est sortit de la cnc 14 allemande cnc14.de/schau...u24o6a5WgtNB3wA
j'espère que la suite de la mise en place se passe bien de votre coté très chouette d'avoir motivé un fablab local, bonne continuation a votre équipe
Hé bravo
! (en plus : atelier rangé, re-
!)
Super félicitations. Réalisation impressionante.
Un projet commencé il y 5 ans, ça doit faire très très plaisir quand ça commence à marcher.
Bravo!
Et y a même le réglage du z0, et l'éclairage de la zone de travail??
C'est le grand luxe!
Une question pratique, tu fais comment pour la ramener, elle a pas l'air petite, la bête.
LionelDraghi Oui, en effet, cela fait plaisir!
Il faut aussi que l'on rajoute un système pour fixer le tube de l'aspirateur.
Cette machine est le fruit d'un travail collectif. Elle appartient au collectif, et sera installée dans un local de l'un des fablabs.
Pour la transporter depuis mon atelier, on l'avait portée à 3, puis, dans une remorque.
Le projet est vraiment top! Je ne sais pas pourquoi plusieurs personnes ont repondu comme si tu avais l'intention de breuveter ta CNC machine en bois ou de l'utiliser pour une usage professionel mais en tout cas un grand bravo pour se projet qui a du etre bien marrant a realiser!
mx92 Il n'y a en effet rien à breveter, et ce n'est pas une machine destinée à un usage professionnel. Ceci dit, avec une électronique et motorisation plus puissante, je pense qu'elle pourrait fort bien convenir à un usage pro intensif.
Génial, elle fonctionne !
Quelles sont les références de l'électronique ? Moteurs PAP, drivers et carte de contrôle ?
toitetmoi C'est du Xtz56 couplé à un MSX 42 et 3 driV33... ou à peu près...
Bon, en fait, cette partie, pour moi, c'est du chinois... Donc, j'ai laissé faire les sachants. Mais je vais me renseigner...
Bravo pour cet achèvement

Bravo!!! impressionnant!! tu ne vas plus avoir de limites maintenant

Vic66 Je te dis pas la liste des choses que je veux faire...
Pollux à cause de la brosse de l'aspiration?! non!?
Vic66 Yes!
Je repost un commentaire suite a la mise a jour avec le rendu final. C'est absolument top! Vraiment bien fait et les coupes ont l'air hyper precises. Bravo et amuses toi bien avec!
PS: Tu utilise quel soft pour la partie CAD/CAM?
Merci. On utilise Cambam / grbl.
Elle serais pas montée sur des castors ta CNC en bois ?
Rien que voir Môssieur Kentaro content comme un gamin à Noël ça vaut son pesant de contreplaqué
Bravo pour l’abnégation, le joli clin d’œil à Kentaro San et la chouette collaboration avec les fablabs.
Raoul222 ça tu peux le dire, je suis content comme un gamin...
C'est aussi bien que mon train électrique Lego!
ben !!!!!!!
Fais-nous plutôt la liste de courses pour fabriquer la même ! Et le mode d'emploi...
Ara
La liste des courses pour la fabriquer, elle est dans le pas à pas, non ?
Bâti:
Motorisation (c'est pas moi qui m'en suis occupé...):
On trouves des kits sur aliexpress autour de 300/400 €.
Broche à 200 € sur Aliexpress, ou en attendant, Affleureuse makita
Pilotage de la machine:
cambam /grbl (voir les tutos sur le Tioube)....
Kentaro oui, oups !
Franchement génial. J'avais en projet d'en construire une avec mes étudiants en architecture ici, c'est pas.encore tombé dans les oubliettes mais je n'avais pas ma certitude qu'en bois ça serait une bonne option (et pourtant je suis un grand fan de voiliers en contreplaqué...). Le principal problème ici en Côte d'Ivoire est de trouver du CP de qualité. Mais ça travaille dans la tête, on va y arriver. Merci, merci, merci pour ce partage super documenté.
GuBragh Le cp utilisé pour les caissons est un cp bas de gamme pas cher (140 € pour le bâti). Et cela n'a pas bougé. Donc, en bois, c'est faisable et ça marche!
On peut aussi commencer par une structure en bois, pas nécessairement au top, puis, modifier, changer des morceaux au fur et mesure, en fonction de l'argent dispo.
Une machine, c'est évolutif, et il ne faut pas nécessairement viser le top dès l'origine.
Merci beaucoup, tu me rassures. On peut avoir ce qu'on appelle 1er choix sur le marché local, on en fait des meubles, ça tient à peu près le coup. Je me disais qu'en le saturant d'epoxy, comme on le fait en construction navale, ça peut aider. Mais je n'en ferais pas un bateau pour faire le tour du monde.
GuBragh tu es où en Côte d'Ivoire ? J'y ai passé trois ans, à Abidjan, dommage qu'on ne se soit pas croisé.
Tu peux trouver du contreplaqué de bonne qualité chez DMD. Bon, deux à trois fois plus cher que le local mais ça permet de fabriquer des trucs qui durent dans le temps
toitetmoi Bonjour, désolé, j'étais sur d'avoir déjà repondu... Je suis à Abidjan. En effet, ça aurait pu etre sympa de se croiser. Mais ce n'est peut-etre que partie remise ? Moi j'y suis pour longtemps (toujours ?)... DMD je ne connais pas, mais je vais explorer. Ce que j'ai pu avoir comme CP "premier choix" est franchement moyen, et c'est souvent du fromager ce qui n'est vraiment pas terrible comme bois.
GuBragh
J'y étais entre 2018 et 2021, mais même si j'ai beaucoup aimé ces trois ans, c'est pas gagné que j'y retourne à long terme (mais sait on jamais ce que la vie nous réserve). Tu trouveras DMD à Marcory sur le VGE, et également à Yopougon dans la zone industrielle. Ils vendent pas mal de choses, à un tarif plus correct que Bernabé. Reda, le patron, est très sympa, tu peux aller négocier avec lui directement. Il t'offre aussi le café s'il est dispo.
toitetmoi en effet on aurait pu se croiser.moi j'y suis arrivé en 2016, j'ai fait le suivi architectural du chantier de l'Hôpital Mère Enfant de Bingerville pendant deux ans, et petit à petit j'ai pris racines... J'irai voir DMD, je suis à Marcory presque tous les matins.
Vraiment génial cette réalisation ! Ca donne envie, ca fait rêver !
Un énorme avantage que je vois aujourd'hui a ton exemple c'est le cout qui reste abordable pour se décider a se lancer. Il est très raisonnable et peut permettre de "rentabiliser" rapidement sa construction avec ces premières réalisation, pour un amateur bien sur.
Bravo pour la réalisation et le partage !
lolovi Oui, c'était vraiment l'objectif de faire un truc low cost, qui marche bien.
Cela coûtera peut-être un peu plus maintenant, avec l'explosion des prix des matériaux, mais cela restera raisonnable.
La bâti, c'est facile à faire pour un boiseux. Après, pour l'électronique, il faut connaitre, ou trouver quelqu'un qui connait.
Super, super top. Quel projet fabuleux ! Idéal pour ceux qui peuvent travailler avec toi au fablab, les "veinards".
Kentaro je reviens un peu là-dessus, j'ai lancé l'idée de constuire une CNC dans le cadre d'un projet pour mez étudiants à l'école d'architecture d'Abidjan, ou j'enseigne accessoirement - j'aimerais bien leur faire dessiner des plans, et fabriquer la machine après. On n'a pas forcément accès à tout ce à quoi on rêve ici. Pour des accessoires métalliques on va probablement etre obligés à se tourner vers Alibaba ou au mieux un serrurier local. Comme je le disais il y a quelque temps le CP qu'on trouve un peu plus facilement est du fromager, très mauvaise qualité, plein de vides dans les collages et bois très... "light" pour rester poli. Est-ce que tu penses que du CP bakélisé peut faire l'affaire ? Pour nous ça serait de l'import, mais au moins on aurait une base fiable... J'en ai vu à environ 30 000 F.CFA la feuille en 18mm, ça revient à environ 45€, ça parait cher mais du CP basique reviendrait à 10-12 000 F.CFA (donc 15-16€ la feuille) et c'est beaucoup moins fiable. Un avis s'il te plait ?
GuBragh Le cp bakelisé irait très bien. Je ne connais pas le cp de fromager, mais en fait, si on fait des boites de torsion, autorigides, je n'ai pas l'impression que cela va beaucoup bouger, même avec un truc de mauvaise qualité.
De plus, tout dépend de la précision que tu attends.
Enfin, je le dis toujours, on ne fait pas des choses qui doivent tenir le temps des pyramides ni des machines pour aller sur Mars... Donc, on fait avec ce qu'on a, et si dans quelques années, c'est tout tordu, on refait... De toute façon, ce qui est important et intéressant, c'est de faire le truc...
Pour les rails, et les vis d'entrainement, j'ai donné les liens où les trouver.
Merci beaucoup ! C'est sur que le plus important, c'est de faire le truc, c'est bien pour ça que je voudrais m'inscrire dans une espèce de projet plus ou moins pédagogique. On verra bien, j'ai lancé l'idée hier auprès du DG de l'école, mais même sans son aval on pourra le faire en temps caché. En tout cas je publierai des news de l'aventure si on arrive à la lancer.